What Is Concrete Batching Plant
Concrete batching plant, also called briefly batch plant or batching plant, is a construction applied equipment that mixes concrete. It used to combine coarse aggregates, sand, cement, and other admixture to produce homogenous concrete. The final mixture can be widely used to construct skyscrapers, sidewalks, bridges, houses, highways, airports. etc. The plants can be used wet or dry, and come in a variety of configurations and production types
Batching plant capacity ranges from 25m³/h to 240m³/h, largely depending on the types of concrete batch plants and concrete batching plant design. For instance, The size of stationary batching plants is commonly larger than that of mobile ones.
How many types of concrete batching plants are there? To learn about or to purchase concrete batch plants, figuring out the classification of them is undoubtedly the most primary and critical step. The classification methods of concrete plants nowadays are so diverse and complex that some confusion may arise in your mind from time to time. The following summary will help you tackle this problem.
Types of Concrete Batching Plant
Classification Basis | Type A | Type B |
---|---|---|
Structure | Stationary | Mobile |
Mixing Mode | Batch | Continuous |
Process Layout | Single-stair | Double-stair |
Water-adding Mode | Ready-mix | Central-mix |
Mixer | Twin-shaft Horizontal | Planetary Vertical |
Specifications
Type | HZS25 | HZS35 | HZS50 | HZS75 | |
Theoretical production capacity(m³/h) |
25 | 35 | 50 | 75 | |
Aggregate Bin volume(m³) |
2/3×3.2 | 2/3/4×7.3 | 2/3/4×8.3 | 2/3/4×12 | |
Weighing Accuracy |
Aggregate (KG) |
1500Kg ±2% | 2200Kg ±2% | 3000Kg ±2% | 4500Kg ±2% |
Cement(KG) |
300Kg ±1% | 450Kg ±1% | 600Kg ±1% | 1500Kg ±1% | |
Fly ash(KG) |
400Kg ±1% | 600Kg ±1% | |||
Water (KG) |
200Kg ±1% | 200Kg ±1% | 400Kg ±1% | 600Kg ±1% | |
Additive(KG) |
30Kg ±1% | 50Kg ±1% | 50Kg ±1% | ||
Discharging height(M) |
3.8 m | 3.8 m | 3.8 m | 4.1m | |
Gross weight(T) |
10 | 15 | 40 | 50 |
Type | HZS60 | HZS90 | HZS120 | HZS180 | HZS240 | |
Theoretical production(m3/h) | 60 | 90 | 120 | 180 | 240 | |
Aggregate Bin volume(m3) | 8.38 | 12 | 20 | 30 | 40 | |
Belt conveying Capacity(t/h) | 300 | 450 | 550 | 650 | 900 | |
Weighing Accuracy | Aggregate (KG) | 3000Kg ±2% | 3000Kg ±2% | 2200Kg ±2% | 3000Kg ±2% | 4200Kg ±2% |
Cement(KG) | 1500Kg ±1% | 1500Kg ±1% | 1200Kg ±1% | 1800Kg ±1% | 2200Kg ±1% | |
Fly ash(KG) | 600Kg ±1% | 900Kg ±1% | 400Kg ±1% | 500Kg ±1% | 800Kg ±1% | |
Water (KG) | 600Kg ±1% | 600Kg ±1% | 500Kg ±1% | 800Kg ±1% | 1000Kg ±1% | |
Additive(KG) | 50Kg ±1% | 50Kg ±1% | 50Kg ±1% | 80Kg ±1% | 80Kg ±1% | |
Total power(KW) | 120Kw | 165Kw | 130Kw | 170KW | 220KW | |
Discharging height(M) | 3.8 m | 4.1 m | 4.1m | 4.1m | 4.1m |
How Does A Concrete Batching Plant Work
Concrete batching plant is a kind of combined device, mainly composed of main building structure, mixer, powder silo, screw conveyor, belt conveyor, weighing system, liquid supply system, gas supply system, electric control system, dust removal device, batching station, control room, used for centralized production of concrete.
Despite the difference in the size of the stationary concrete batching plants and the mobile ones, both have the same working principle.
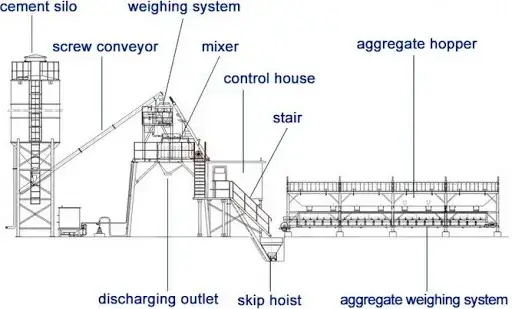
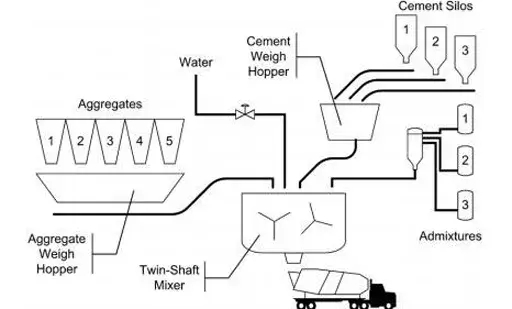
Concrete Batching Plant Process Flow
Batching Plant Operation Procedure
1. Load the aggregates like gravel and sand into individual storage bins, and after being weighed individually, they will be dispatched to the feeding belt conveyor, which then convey them to the weighing hopper on the top of the concrete mixer.
2. Under the control of the control system, the cement is transported to the weighing hopper by the screw conveyor; the water and additives are also transferred to their respective weighing hoppers.
3. Open the pneumatic door of the weighing hoppers; open the pneumatic butterfly valve of the cement weighing hopper, fly ash weighing hopper, and the water weighing hopper; Open the pneumatic ball valve of the additive weighing hopper.
4. Turn on all the weighing hopper vibrators and water inlet pressure pumps to make all materials enter the concrete mixer to blend evenly.
5. Once the setting time is over, the mixer will discharge the mix into a transit mixer or a concrete pump.
Please keep in mind that commonly the concrete must be prepared, transported, and then applied between 30-45 minutes, which is also known as preparatory setting time, concrete must not segregate in the whole course.
Advantages of Concrete Batching Plants
Preparing ready mix concrete on the construction site is a time-consuming process. You can eliminate your construction cost by using a batching plant for your project. Each load of concrete is produced on-site. The production and delivery are done in minutes when we use a concrete batching plant. Adjust your concrete production as per the requirements and get the most out of it. There are several benefits that the concrete batching plant has to offer to construction workers:
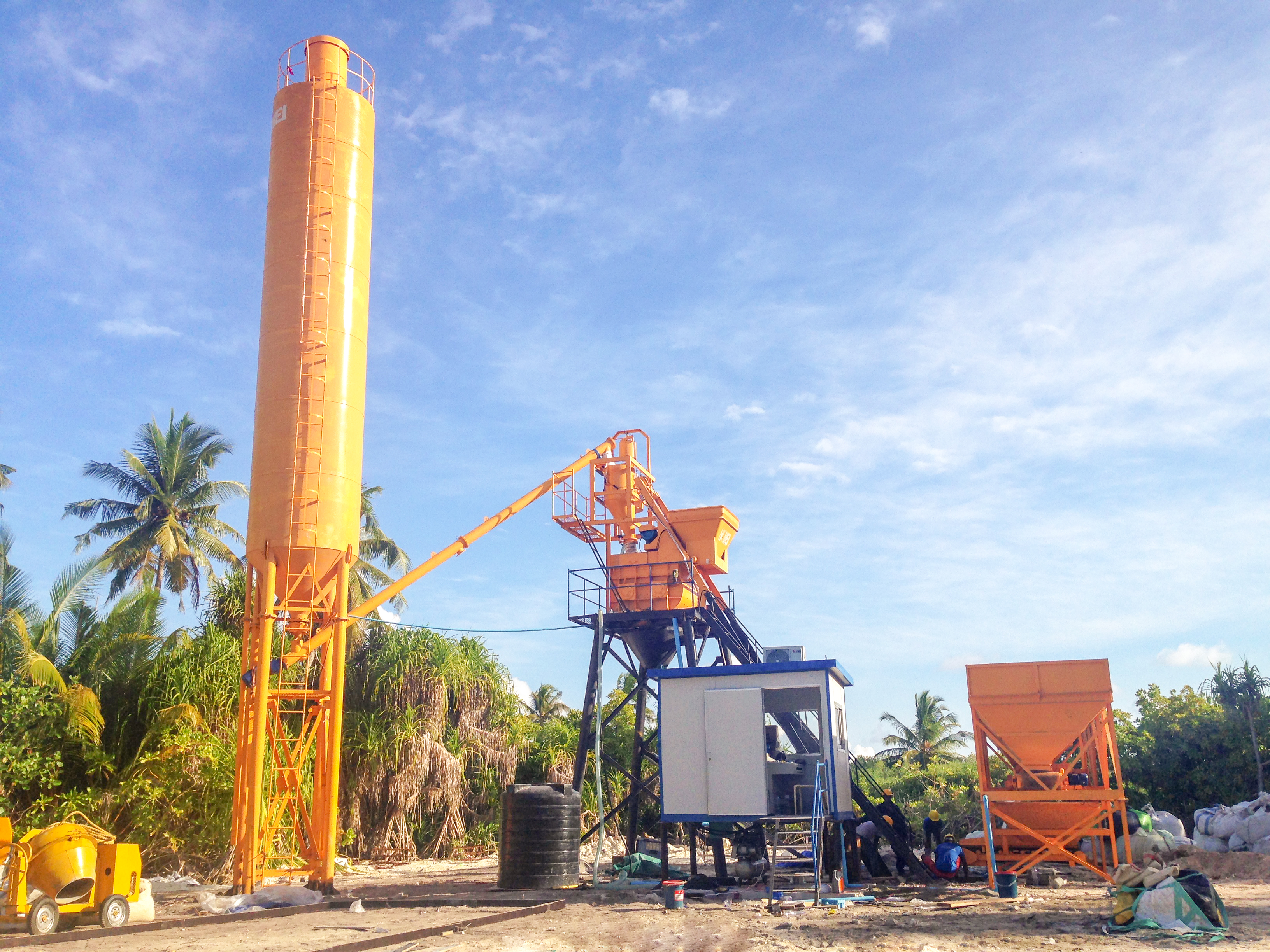
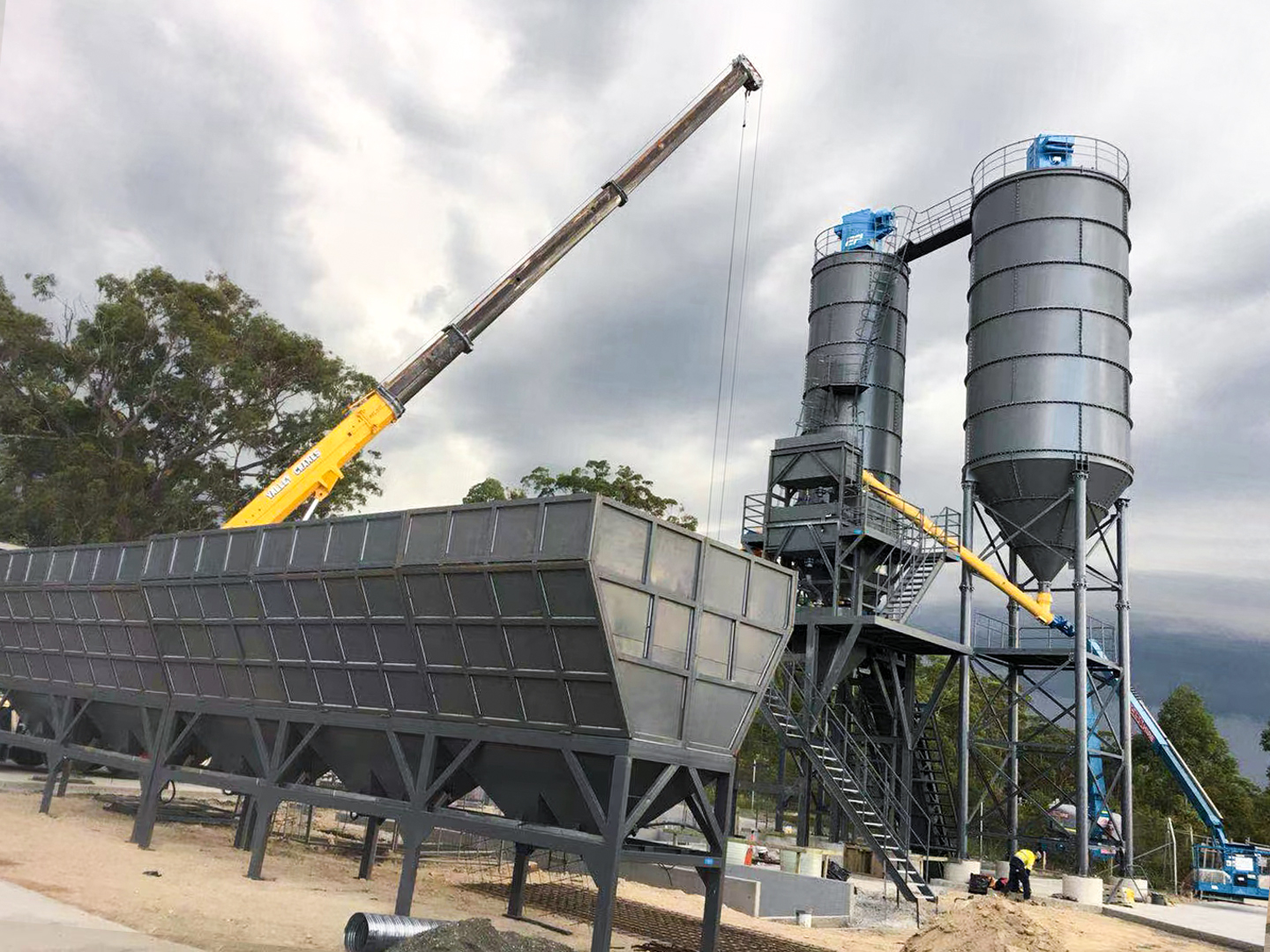
Mixing raw materials with stable, advanced production technology, using computer control, accurate measurement, testing means complete, stable and reliable quality, rich high strength, thus greatly improving the construction quality level building (structure).
Construction units use commercial mixing stations, the construction speed increases, reducing equipment, racks, pipes, templates and other turnover rental costs; owners of units can shorten the construction cycle, reduce investment risk.
Due to the stable and reliable quality of the commercial mixing plant, the design unit can avoid the “fat beam”, “fat column” and “heavy plate” according to the design of the mixing station”.
The mix mixing station using mineral active admixtures (slag and fly ash and admixture, etc.) can greatly improve the long-term performance of concrete waterproof, antifreeze, anti cracking and abrasion resistance, and can improve the service life of a building.
Improves the construction organization, reduces labor intensity, reduces construction management costs, technical difficulty and quality risk.
Batching Plant Inspection Checklist
How to check the quality of the concrete batch plant, what should be paid attention to before the first use of your concrete plant, the answers to these critical questions are summed up by us as follows.
1. Inspect the quality of the steel bars, the size of the mesh, and the accuracy of the screening when it comes to vibrating screen.
2. To see whether the work of the transmission system is active and whether there is any abnormal noise.
3. The transmission of belt conveyors, bucket elevators, and cantilever drag shovel should be stable, with no abnormal noise, no jamming.
4. Examine the flexibility and accuracy of the measurement system.
5. Observe whether the rate of temperature rise of the reducer is aligned with the qualification certificate or not.
6. Material's In and out through the measuring hopper should be smooth, with no signs of accumulation, overflow, etc.
7. The safety valve cannot show air leakage.
8. Check whether the quality of the cement tank is qualified.
9. The circuit equipment should be reasonable and accurate.
Frequently Asked Questions (FAQs)
-
What distinguishes a concrete batching plant from a traditional concrete mixing method?
Unlike traditional concrete mixing methods that involve manual measurement and mixing, a concrete batching plant automates the entire process. It precisely measures and combines aggregates, cement, water, and admixtures based on a predefined mix design, ensuring consistent and accurate results for large-scale concrete production. - Can a concrete mixing plant accommodate customized concrete mix designs? Yes, modern concrete batching plants are designed to accommodate a wide range of concrete mix designs to suit diverse construction requirements. The control systems allow operators to input specific ratios of aggregates, cement, water, and admixtures, enabling the plant to produce customized mixes with precision.
-
How does a concrete batching plant contribute to sustainability in construction?
The batching plants contribute to sustainability by optimizing resource utilization. Advanced control systems monitor ingredient measurements, minimizing wastage and ensuring efficient use of materials. Additionally, the ability to produce consistent and high-quality concrete reduces the need for rework and enhances the durability of structures, promoting longer service life and reduced environmental impact. -
Can a batching plant be relocated for different construction projects?
Yes, many concrete batching plants are designed to be mobile or semi-mobile, offering the flexibility to relocate to different construction sites. This mobility is particularly advantageous for construction businesses engaged in projects at varying locations. Mobile batching plants can be transported to the site, set up quickly, and start producing concrete, saving time and resources. -
How does a concrete batching plant ensure consistent quality in the produced concrete?
Concrete mixing plants ensure consistent quality by automating the measurement and mixing processes. The advanced control systems closely monitor ingredient proportions, mixing times, and other parameters, reducing human error and variations. This precision guarantees that each batch of concrete meets the desired strength, durability, and other performance criteria. -
What safety measures are in place within a batching plant?
concrete batching plants prioritize safety through various measures. These include safety guards on moving parts, emergency stop buttons, proper ventilation systems to mitigate dust and fumes, and employee training on plant operation and safety protocols. Occupational health and safety standards are upheld to ensure a secure working environment for plant operators and personnel. -
Can a batching plant be integrated with other construction equipment?
Yes, concrete mixing plants can be integrated with other construction equipment, such as concrete pumps, mixers, and conveyors, to streamline the construction process. The integration allows for the seamless transfer of freshly mixed concrete to the construction site, enhancing efficiency and reducing manual handling. -
How does a concrete batching plant contribute to project scheduling and timelines?
concrete batching plants play a crucial role in project scheduling by providing a consistent and reliable supply of concrete. With precise control over production, construction businesses can better plan and manage their concrete requirements, minimizing delays and ensuring timely project completion.